What is injection moulding?
The majority of our products in the bucket and cup categories are manufactured using the injection moulding process.
An injection moulding machine essentially consists of a nozzle, moving clamping plate, fixed clamping plate, feed hopper, screw (or plasticising screw), ejector unit, locking mechanism and console.
The hopper feeds plastic granulate to the screw. The high temperature in the injection unit melts the plastic material (up to 200°C is possible).
The screw feeds the material to the injection barrel, where the liquid plastic is injected into the mould under high pressure. This injection takes place in two stages - the injection phase and the holding phase. The material is injected into the closed mould (cavity), where it cools and solidifies.
At the same time, the material for the second injection is fed into the screw from the hopper.
After cooling, the parts are ejected from the mould. The closing mechanism of the moving platen then seals the mould back to the mobile half of the mould. A new cycle can be started.
Additional Information
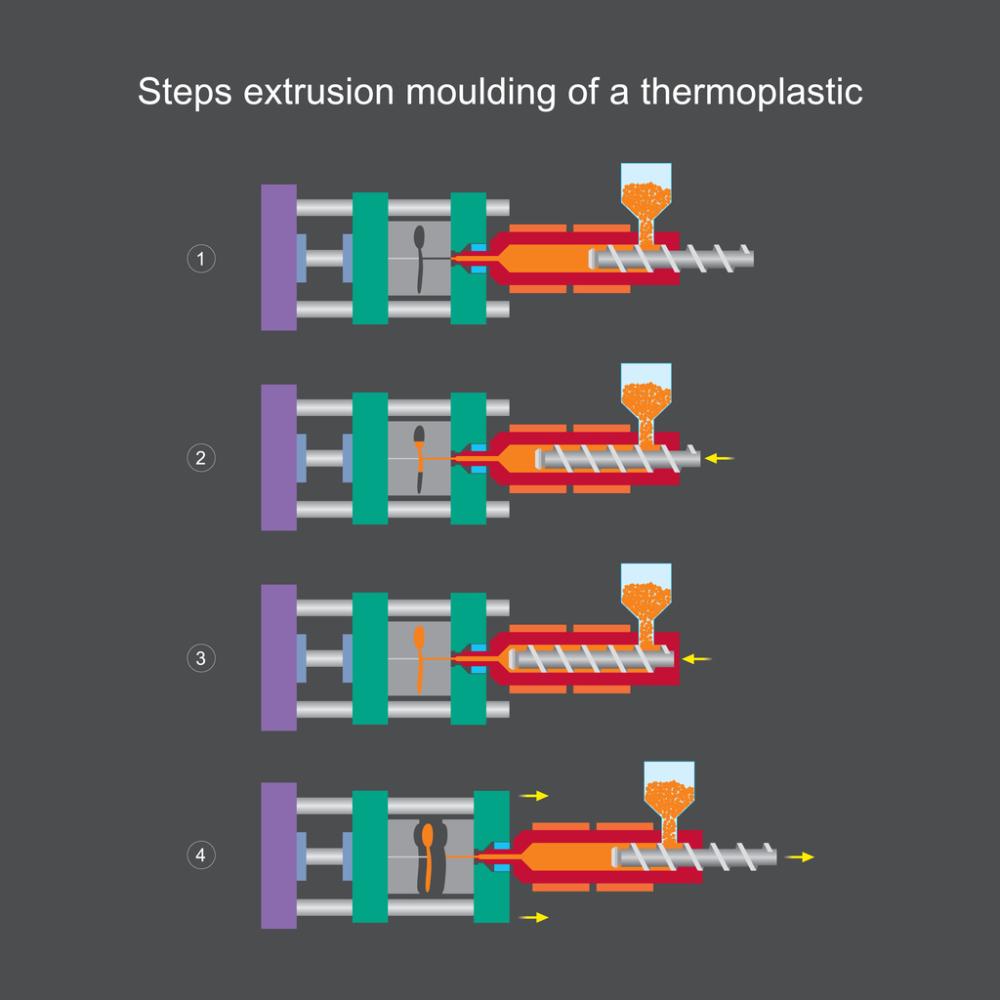